2024 Awards
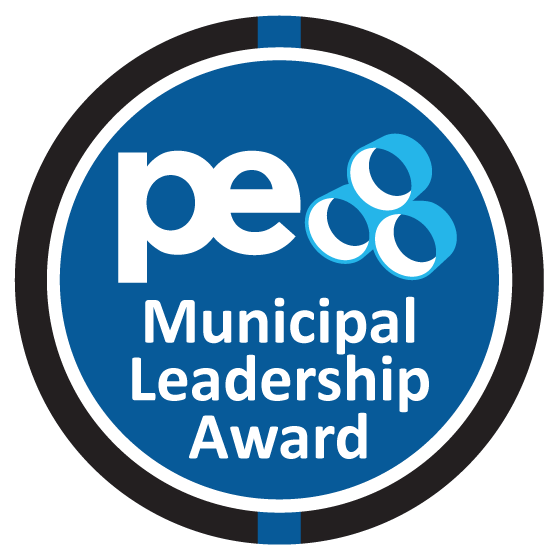
2024 – CREATIVE TRENCHLESS INSTALLATION
The Unified Southern Sarpy Wastewater Project
Sarpy County and Cities Wastewater Agency
19 Miles | 14” to 36” HDPE Dual Force Mains | DR 17 DIPS
Presented to ISCO Industries
Submitted by Will Vodak
Sarpy County, Nebraska, faced development challenges due to limited infrastructure. The $130 million Unified Southern Sarpy Wastewater Project addressed this with 19 miles of sewer lines, including 17 miles of 14” to 36” HDPE dual force mains and three lift stations.
HDPE pipe played a key role, enabling efficient installation through Horizontal Directional Drilling (HDD) to overcome roadways, railroads, and other obstacles. The project opens 70,000 acres for development, supports 40 years of growth, and is expected to create over 4,500 jobs while driving billions in economic impact.
2024 – INNOVATIVE PE SOLUTIONS
West Ouachita Sewerage District No. 5
West Monroe, Louisiana
7,500 Feet | 24” HDPE Force Main | DR 11 DIPS
Presented to: Industrial Utility Sales Company
Submitted by: Joshua Hays, P.E., Lazenby and Associates
Participating Members: J.S. Haren Company, Lazenby and Associates
West Ouachita Parish in West Monroe, Louisiana, is in the second phase of replacing an 18” ductile iron force main sewer pipeline with 24” HDPE pipe. The original ductile iron system, installed in 1976-77, began experiencing leaks within 30 years due to the area’s highly corrosive soils. Phase one of the replacement began in 2005, addressing the northern section, and phase two is currently underway due to continued leakage and maintenance issues.
The second phase, with a budget of $1.4 million, will replace a significant portion of the pipeline, which serves 8,000 people in West Monroe and additional surrounding areas. The upgraded system is expected to reduce leaks, eliminate odors, and provide a corrosion-resistant, reliable solution for handling 1 to 1.5 million gallons of wastewater daily.
Ken Downey, Superintendent of Installation for JS Haron, praised HDPE for its toughness, durability, and flexibility, enabling pre-assembly of large sections for quicker installation, even in adverse weather conditions. Horizontal directional drilling (HDD) was used for crossings under roads and railways, despite higher costs, as it minimizes disruptions and long-term expenses.
Once completed, two-thirds of the pipeline will benefit from HDPE’s reliability, while the remaining ductile iron sections are expected to require replacement in the future due to anticipated leaks. The project highlights HDPE’s advantages in durability, efficiency, and cost-effectiveness for infrastructure upgrades.
2024 – INNOVATIVE PE SOLUTIONS
Baltimore National Aquarium Harbor Wetlands
National Aquarium
2080 Lineal Feet of 26-inch IPS DR 32.5 HDPE Pipe
Presented to ISCO
Submitted by: Cesar Gallardo
Participating Members: Coastal Marine Construction, JM Eagle, Performance Pipe
The “Inner Harbor” in Chesapeake Bay, once a thriving tidal wetland marsh, has been transformed over time by docks and bulkheads due to urbanization and industrialization. In the late 2000s, the National Aquarium began efforts to restore this critical habitat, culminating in a third HDPE prototype built in 2015 that utilized HDPE technology, which remains in use today due to its durability and flexibility.
In July 2022, ISCO engaged with Coastal Marine Construction and the Aquarium to advance the project. A year later, ISCO played a key role in designing and supplying 208 HDPE floats. These floats feature two 26-inch HDPE pipes acting as pontoons, allowing ballast adjustments to accommodate growing flora and maintain platform stability. This design prevents the platforms from sinking while keeping them level with tidal changes, enabling maintenance and educational activities.
ISCO’s HDPE floats set this project apart, providing resilience in brackish water and ensuring a consistent, durable solution. Despite a six-month production schedule, ISCO delivered the floats in just five months, including on-site welding of 30 one-inch ports to meet the Aquarium’s timeline. This collaboration between the National Aquarium, Coastal Marine Sciences, and ISCO demonstrates the innovative use of HDPE in habitat restoration, ensuring both functionality and sustainability in reviving this historic ecosystem.
2024 – FIRST-TIME USER
Pronghorn Crossing Subdivision
Moyes Family Homes
2000′ of 8-inch IPS DR 11 & 17 HDPE Pipe
Presented to Secor
Submitted by: Chris Weight
Participating Members: Moyes Family Homes, Rio Verde Engineering, WL Plastics
This project, completed between June and September 2024, installed 2,000 feet of water main and 1,800 feet of sewer line. It marked the first time Moyes Family Homes and the City of Pinedale utilized HDPE. They chose this material to reduce costs and address key issues, such as infiltration problems associated with ductile iron and a significant 15%+ water loss rate.
The project served a new subdivision, providing essential infrastructure for 36 homes, and achieved notable efficiencies, cutting construction time by two months. High groundwater levels posed a significant challenge, but HDPE proved ideal, allowing pre-chlorination above the trench before installation to streamline the process and ensure quality results.
2024 – DEDICATED USER
Tishomingo Water Well Transmission Line
City of Tishomingo
50,000 ft of 16-inch DIPS DR 11 HDPE Pipe
Presented to Pipeline Plastics
Submitted by: Stephen Boros
Participating Members: Wall Engineering, Milford/Winn Supply
Tishomingo, Oklahoma, located in southeastern Oklahoma, serves as the capital of the Chickasaw Nation. To support future economic development, the city recognized the need to increase its water supply. Drawing on prior experience with HDPE pipe in golf course applications, the city manager was familiar with its durability, resilience, and cost-effectiveness. Confident in its advantages, the city procured HDPE pipe for a new well source located approximately 10 miles away, even before the project’s design was fully finalized a year later.
2024 – ENVIRONMENTAL SUSTAINABILITY
James River Crossing
Hampton Roads Sanitation District (HRSD)
>18,500 LF of 48″ and 54″ HDPE Pipe (DR-11, DR-15.5, DR-17)
Presented to AGRU America, Inc.
Submitted by: Yuse Lajiminmuhip
Participating Members: Garney Construction, High Country Fusion
In 2018, the Hampton Roads Sanitation District (HRSD) launched the $2 billion Sustainable Water Initiative for Tomorrow (SWIFT) program to address long-term groundwater sustainability in the region. The project aims to treat highly purified wastewater and reintroduce up to 120 million gallons per day into the Potomac Aquifer, ensuring a stable groundwater supply while reducing discharge to surrounding rivers.
Garney Construction is leading the design-build effort, including a new equalization and pumping facility, advanced SWIFT treatment, recharge wells, and a transmission force main. The project features a record-setting horizontal directional drill (HDD) and subaqueous installation of AGRU-manufactured 54” and 48” HDPE pipes, supported by precast concrete ballast blocks.
A 90’-long reach excavator and cranes equipped with clamshell buckets will install the subaqueous pipes, fused on a barge and sunk into a trench. After landfall is achieved in summer 2025, the pipeline will be backfilled and reinforced with armor-corrugated block mattresses (ACBM). This ambitious effort addresses regional water needs while showcasing advanced engineering techniques.
2024 – ENVIRONMENTAL SUSTAINABILITY
VinFast Auto Plant Infrastructure
VinFast Automotive
>150,000 feet of HDPE Pipe (Water, Sewer, Gas, Conduit)
Presented to WL Plastics
Submitted by: Dustin Langston
Participating Members: Core and Main, Ames Construction
WL Plastics supplied all HDPE pipe for the new VinFast EV auto plant in Chatham County, South Carolina. In exchange for VinFast’s $4 billion investment, which promises 7,500 new jobs, state and county governments committed to delivering essential utilities, including water, wastewater, telecom, and natural gas, to the plant.
The project required over 50 miles of HDPE pipe in various sizes, including 10 miles of 36”, 1 mile of 24” and 2 miles of 16” DR11 blue stripe, 5 miles of 36”, 10 miles of 24” and 2.5 miles of 18” DR21 green stripe. In addition, 15 miles of conduit for fiberoptic and natural gas distribution. Pipe was shipped from four of WL Plastics’ ten plants, showcasing the material’s versatility and rapid supply capabilities.
Originally designed for ductile iron, the project specifications were changed to HDPE due to faster availability and installation speed. The scale of construction was immense, with 28 million tons of soil moved to prepare the site. This project highlights the efficiency and adaptability of HDPE in meeting complex infrastructure demands for large-scale industrial developments.