Fort Lauderdale
This is a great story for the citizens of Fort Lauderdale, Florida and the HDPE community. In 2017, the PE Alliance, ISCO an Murphy Pipelines collaborated on a roadshow in Sunrise, Florida, which is 11 miles from Fort Lauderdale. Four engineers from Fort Lauderdale attended the show, listened to presentations, and watched Murphy Pipelines install HDPE pipe via pipe bursting of AC pipe during the live, afternoon exhibition. A few short months later, a sewer force main in Fort Lauderdale burst, causing millions of gallons of raw sewage to pollute the Intracoastal Waterway. Following some research, Fort Lauderdale engineers embarked on a $65 million HDD project utilizing HDPE pipe.
Three years after the completion of the ambitious project, city engineers told the PE Alliance during a 2023 roadshow in neighboring Davie that the city’s standard specification now includes HDPE pipe and they use it on most every project in their capital plan. The city’s emergency use of HDPE pipe directly led to their better understanding of the product and their commitment to best serve the 182,000 citizens of their coastal city.
The Fort Lauderdale $65 million dollar, emergency Design-Build project is one of the most ambitious directional drilling projects to be installed within a downtown environment. The fast-tracked project installed 39,000 feet of 48 and 54-inch HDPE pipe, utilizing 17 large directional drills and staying 91% trenchless. Murphy Pipelines played a critical role in this project as both educator and contractor.
The project received the PPI 2021 Trenchless Project of the Year and the 2022 Alliance for PE Pipe Innovative Trenchless Award. HDPE is ideal to safely cross through Environmental sensitive areas. For example, The crossing of South Florida’s Intracoastal required Benthic Surveys to identify and protect local ecosystems, which required permitting through the U.S. Army Corps of Engineers.
- Substantial permitting was required through 11 jurisdictional agencies, which included Municipal, County, State, and Federal regulatory agencies.
- Thermosetting resins were injected into the ground to prevent borehole collapse in sensitive areas.
- The large scale of the project required calculations for temperature changes and pipe expansion and contraction.
- Electrofusion restraint saddles were installed to limit axial pipe movement.
Horizontal Direction Drilling was the primary installation method used. Of the 17 HDDs, the most impressive were:
- The installation of 3,400 feet of 48-inch HDPE DR (Dimension Ratio) 13.5 pipe.
- The installation of 3,100 feet of 54-inch HDPE DR 17 pipe with 22 fusion welds during pipe pull back.
- Four HDDs with tight-radius compound curves using 48-inch HDPE DR 13.5 pipe, which included a 2,600-foot and a 1,400-foot S-curve.
- Three major waterway crossings (Tarpon River – 1,800-foot HDD, New River – 2,500-foot HDD, and Middle River – 1,600-foot HDD) reaching depths of over 60 feet. Due to depth and soil conditions, a 48-inch DR 11 pipe was used in the Middle River crossing, making this one of the first projects in the United States to utilize this pipe size and dimension ratio.
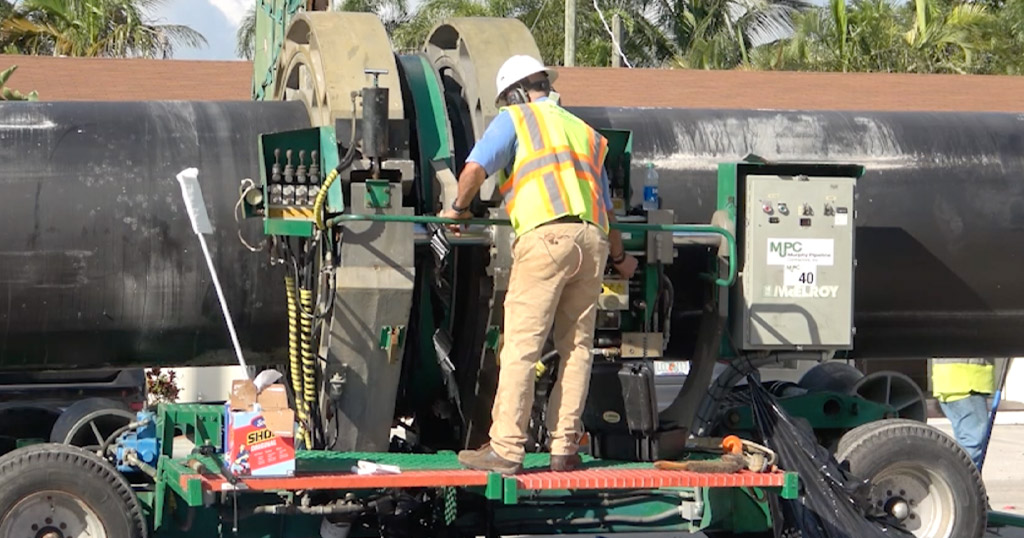
Illustration: clips from the award submission in 2022